3D Printing News Briefs, September 23, 2023: Research Awards, Dental Veneers, Gaming, & More – 3DPrint.com
In 3D Printing News Briefs, technologies developed by ORNL researchers won six R&D research awards, Rolls-Royce delivered its first of four Coach-built Droptail models with 3D printed elements, and Boston Micro Fabrication will market the thinnest cosmetic dental veneer. The Rube-Goldberg marble run was built by an electronics engineer with 200 3D-printed parts and an old bottle of gin. Finally, there’s a new handheld gaming PC that you can 3D print and build at home, and a model kit artist on YouTube 3D printed the ‘hover bike’ design from “The Legend of Zelda: Tears of the Kingdom” video game.
Technologies by ORNL Researchers Receive Six R&D 100 Awards
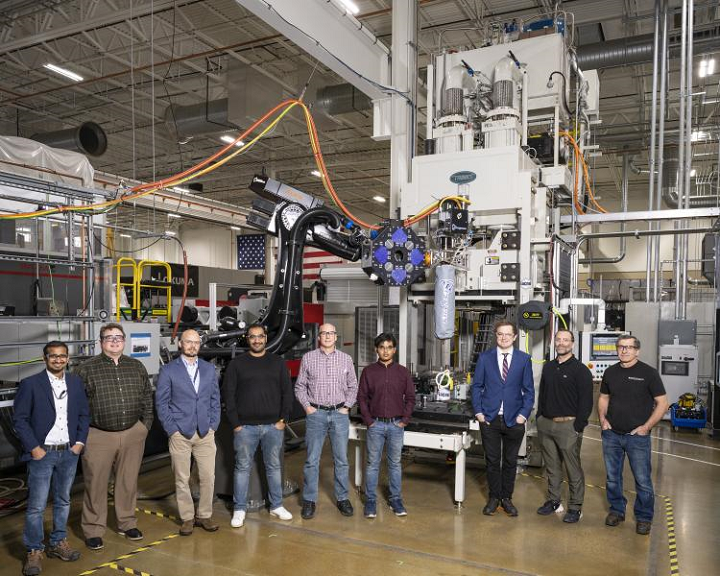
Researchers pictured here at the DOE Manufacturing Demonstration Facility at ORNL developed the R&D 100 Award-winning hybrid additive manufacturing-compression molding, or AM-CM, technology. ORNL, US Dept. Energy
Technologies developed by Oak Ridge National Laboratory (ORNL) researchers have won six 2023 R&D 100 Awards from R&D World magazine. Since 1960, these awards honor science and technology research that results in new products, technologies, or commercial products that can be licensed or sold. The DOE Office of Science provided funding for three of the projects: “Additively Manufactured Thermally Conductive Collimators for Neutron Instrumentation,” developed by ORNL and PolarOnyx; “Physics-Informed, Active Learning–Driven Autonomous Microscopy for Science Discovery,” developed by ORNL and the University of Tennessee, Knoxville; and “SuperNeuro: An Accelerated Neuromorphic Computing Simulator,” developed by ORNL. Another winner was “Precise, Continuous, & High-Speed Manufacturing of Thermoplastic Composites Using Additive Manufacturing-Compression Molding, AM-CM,” developed by ORNL with funding from DOE’s Office of Energy Efficiency and Renewable Energy, Advanced Materials and Manufacturing Technologies Office (AMMTO). “OpeN-AM: A Platform for Operando Neutron Diffraction Measurements of Additive Manufacturing,” developed by ORNL, also won, and received funding from DOE Laboratory Directed Research and Development, Digital Metallurgy Initiative. ORNL also supported the development CANDLE (CANcer Distributed Learning Environment), a collaboration among several DOE laboratories, and the Frederick National Laboratory of Cancer Research.
“ORNL strives to deliver technological solutions for the nation’s toughest problems. This year’s R&D 100 Awards are a reminder of how hard our scientists and engineers work to accomplish that feat,” said Jeff Smith, Interim Director of ORNL.
Rolls-Royce Droptail Model with 3D-printed Features is the first coach-built model.
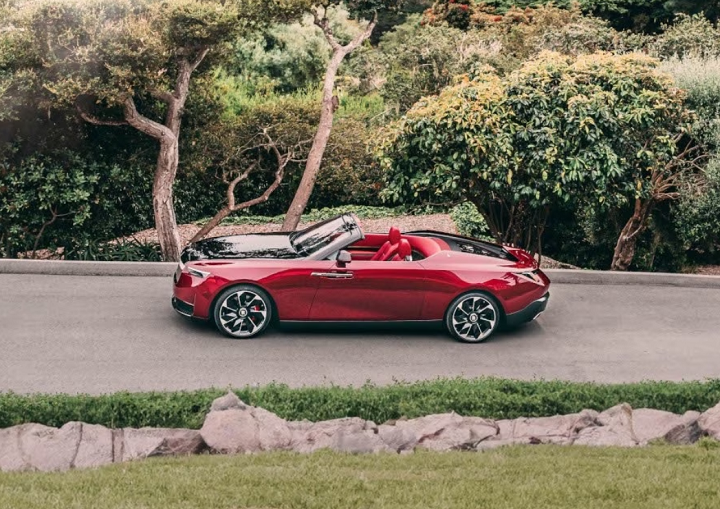
Rolls-Royce La Rose Noire Droptail. Credit: Rolls-Royce
Rolls-Royce presented its first Droptail model, a custom coach-built version. The two-seater convertibles are limited to three and cost over $33 million each. Each of the Droptails will also be unique, as owners pay for a high level of customization; for instance, this first one is named La Rose Noire, in honor of the Black Baccara, which is the commissioning family’s favorite flower. The flower is also the basis of the car’s design, with “petals” represented by red veneer triangles embedded within the black woodwork extending from the instrument panel to the rear deck. The body of La Rose Noire has been painted a shade of metallic black called True Love. Accents such as the removable roof, wheels and hood are painted a deeper red called Mystery.
Once again, Rolls-Royce turned to 3D printing to create some of the Droptail’s customized features. The lower intake manifold was made from composite material and 3D-printed. It was augmented by over 200 ingots of stainless steel, painted in True Love. The twin-turbocharged 6,75-liter V-12 engine is behind the intake, and there’s also a champagne chest in the car made specifically for the owner’s own vintage of Champagne de Lossy. Finally, an exclusive watch, commissioned by the owner’s family from Swiss watchmaker Audemars Piguet, adorns the dashboard, secured by a motorized holder. Once removed, the watch can be worn by the owner. A titanium blank engraved with the Black Baccara is then installed to replace it.
Boston Micro Fabrication Enters Dental Market With UltraThineer
Microscale 3D printing solutions provider Boston Micro Fabrication (BMF) develops applications where its highly-precise projection micro stereolithography (PµSL) technology can reduce cost and production time, and is launching UltraThineer, which it calls the world’s thinnest cosmetic dental veneer. Veneers are currently invasive, uncomfortable and non-reversible because they require the preparation of existing teeth. Developed in collaboration with Peking University, these new durable veneers are only 100 µm thick, which is three times thinner than traditional ones, and dental professionals need much less preparation with them, which allows for preservation of the patient’s enamel. The ability of 3D printing to deliver custom solutions is being used for multiple dental applications. UltraThineer’s veneers, which are made using advanced zirconia and a production process, offer a more comfortable, less-invasive alternative.
“The ability to print ceramics at minimal thickness will be revolutionary. The current methods for creating minimal prep veneers are labor intensive when compared with milled full coverage zirconia crowns. Conservative reduction of the patient’s enamel should be practiced whenever possible,” said Jessica Love from Capture Dental Arts, a leading U.S. provider of cosmetic dental service. “I’m looking forward to the start of this new technology, allowing intricate, ultra-thin veneers to be printed. BMF’s advancements and innovation will continue to push the boundaries of dentistry and inspire innovation worldwide.”
UltraThineer Veneers should be available to the U.S. market by spring 2024, following a review of the FDA.
Rube Goldberg Inspired 3D Printed Marble Run Kinetic Sculpture
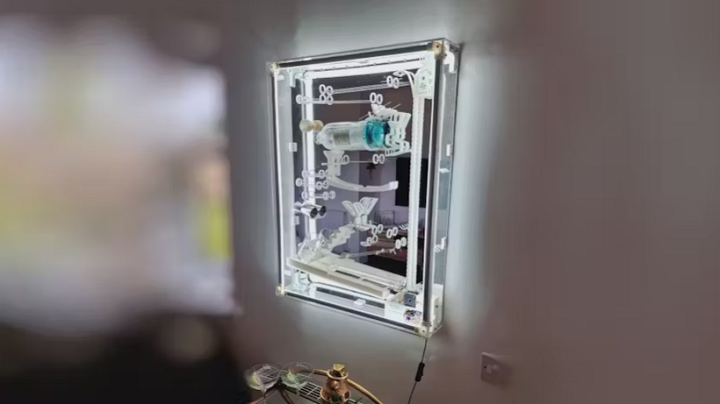
This kinetic sculpture is almost entirely 3D printed, and serves as a homage to the creator’s favorite gin.
David McDaid is an electronic engineer who was inspired to create a 3D marble run kinetic sculpture by Rube goldberg. The piece also pays tribute his favorite gin, made by the Isle of Harris Distillery. He designed the 2D Marble Run in Fusion 360 with the intention of making a piece of art kinetic that could be hung on the wall. It features around 200 individual 3D printed parts, including the lightweight links of a roller chain that brings the marble back to the top after it completes a run, which he called “an absolute pain.” The marble run uses about 250 screws, nuts, and washers, and the empty gin bottle forms part of the structure’s driving mechanism. There’s also a Trinamic TMC2208 stepper motor driver connected to a NEMA17 stepper motor for reducing the noise, and several LEDs, and the whole thing is driven by an Elegoo Nano V3.0 Arduino-compatible microcontroller board and some custom PCBs. McDaid finished the project in about three months.
“There’s only so much testing you can do within a CAD environment, which meant there was a lot of “print, test, repeat” required for each individual component for this build. Revisions ranged from a version one working first try, right up to a version 15 for some non-cooperative parts,” he wrote. “The total amount of filament used during development was around ~2.5kg [around 5.5lbs]. The final build requires only 0.66kg [around 1.5lbs].”
3D Printable NucDeck Handheld Gaming PC
Dan McKenzie, a maker from the UK, created NucDeck – a portable gaming PC you can build yourself at home using 3D printing. It features a 7″ touchscreen display, gyroscopic aiming, analog triggers, RGB joystick surrounds, a battery/controller information screen, and a 4s 3,000mAh Li-ion battery. Combine all of that with a Intel Core-i5-7260U 7th-generation CPU, 16GB DDR4-2133RAM, Intel Iris Plus Graphics 640 custom PCBs and a 3D-printed housing to make your NucDeck. It will cost you around $370. McKenzie designed two versions of the housing. The standard version has RGB joystick surrounds while the NoRGB doesn’t, to make 3D printing easier. He also notes in GitHub that the PCBs and software are incomplete, so you should take this project on “at your own risk!”
“There are two different versions of the buttons, membrane and clicky. The Membrane buttons are shorter and are designed to be used with silicone membranes,” McKenzie wrote on GitHub. “I’ve included files for molds to make the membranes. You should definitely try this with a resin-based printer as it will improve the feel and look of the buttons. FDM printers cannot produce these parts with the precision required. The clicky version is slightly taller and can be used without the membranes.”
Zelda Hover Bike 3D Printed
A few months ago, “The Legend of Zelda: Tears of the Kingdom” video game, also known as “The Legend of Zelda: Breath of the Wild 2,” was released for Nintendo Switch, and it’s just as popular as you’d expect. Fans are busy playing it or paying tribute to it. In one example, a model kit artist from Hong Kong known as ‘qshyj‘ on YouTube turned to 3D printing and an airbrush to recreate the popular hover bike design from the game. It’s one of the top transportation modes in the game because it’s easy to put together: you only need two fans and a stick to switch from riding a horse in the game to riding a hover bike.
From the video, it appears that qshyj used a Creality HALOT-MAGE PRO resin 3D printer to print all the parts for the hover bike, which she designed so they’d all fit in one build. The supports were easy to remove. After that, the parts were UV-cured and sanded. Finally, she painted everything with an airbrush. All the details were painted with paintbrushes or nozzles. Everything was then glued, snapped or glued into place. The work was time-consuming and intricate but the result was well worth it. While it’s definitely not a full-sized vehicle, the handheld replica itself is stunning and lifelike—even featuring the Ultrahand’s “sticky substance” that’s used to connect the devices of the Zonai in the land of Hyrule.
Subscribe to Our Email Newsletter
Receive information and offers about 3D printing from third-party vendors.